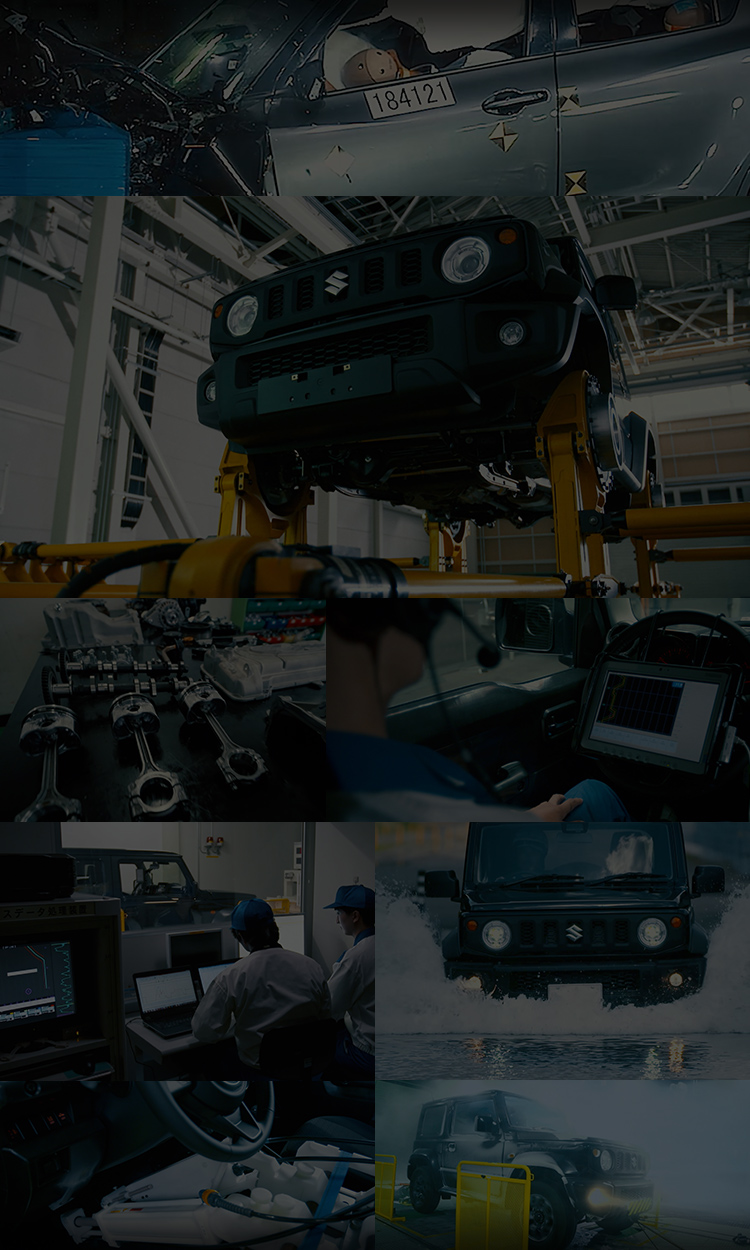
Road simulator endurance testing
In Suzuki’s road simulator endurance test, vehicles and their suspensions are tested for their durability performance. Rough road driving conditions are simulated at a vibration testing facility on which tests are carried out non-stop over several hundred hours. On completion of testing, the vehicles then undergo inspections for damage and cracks.
Climatic wind tunnel testing
In Suzuki’s climatic wind tunnel test, rain and winter driving conditions are recreated to test vehicles for their performance and durability. This facility is capable of simulating not only extreme temperatures and exposure to sunlight, but also heavy rain and blizzards.
Crash test
At Suzuki, crash tests are carried out daily to protect the driver and passengers in the event of a crash. Actual vehicles are used during the test and its body is evaluated. The impact on dummies, the deployment of airbags and the damage on seats and other interior parts are also evaluated. Suzuki’s vehicles combine an indestructible zone for protecting the passenger compartment, and a crushable zone for absorbing impacts.
Aerodynamic testing
In Suzuki’s aerodynamic test, vehicle air resistance is measured in the wind tunnel test. A fan with a diameter of 6 metres generates wind to simulate the air resistance in actual driving situations. Suzuki carries out these tests on vehicles from the clay model stage to optimise the vehicle shape while maintaining its key design. In addition to air resistance, unwanted noise such as those from wind is also measured.
Proving ground
Suzuki vehicles undergo repeated testing at a facility where a variety of road conditions and harsh environments are simulated to ensure safety, comfort and maximum performance under different driving conditions throughout the world.
Components testing
Suzuki carries out tests on the vehicle’s component parts. In this test, a machine is used to automatically open and close doors tens of thousands of times to check their durability and ensure its quality.
Engine dynamometer testing
Engines developed in Suzuki are tested on dynamometers under actual, or sometimes in harsher driving conditions to evaluate their durability, fuel economy and other engine performance. Precise measurements are taken upon controlling a variety of conditions, such as test room temperature, engine oil temperature, engine speed, output power and other testing conditions and driving situations. Development tests in Suzuki are carried out repeatedly to not only ensure safety and quality, but also to enhance output and fuel efficiency.
Air conditioner performance testing
In Suzuki’s air conditioner performance test, testing is carried out at a facility where temperature and humidity are controlled, and heat from sunlight and road surfaces can be simulated. To enhance the performance of air conditioners, tests are carried out from freezing to high temperatures, as well as under various environments and driving conditions, such as high-speed driving and traffic jams.
Anechoic chamber testing
Anechoic chambers are designed to shut out and absorb electromagnetic waves. In Suzuki, tests are carried out to check if unwanted noises are emitted by vehicles and their parts, and also that malfunctions do not occur when irradiated with strong electromagnetic waves.
Chassis testing
Suzuki’s chassis test simulates actual driving situations to test its exhaust emission, fuel consumption and other performance. The wheels are placed on rollers, allowing it to be tested without actually driving the vehicle on real roads. Road surface and air resistance are also simulated to ensure a more accurate recreation of actual driving conditions.